What Is Salt Spray Testing?
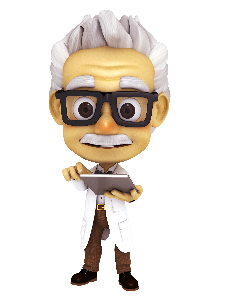
Corrosive Resistance Testing For Industrial Coatings
A Standardised Test To Check Corrosion Resistance
The salt spray test is a standardised test method (UK & Worldwide) used to check the corrosion resistance of coated samples.
The term “coating” may apply to a ‘bare’ surface treatment, a painted finish, or both.
Since coatings can provide high levels of corrosion resistance to metallic parts made of steel, mazak or brass through the intended life of the part, it is necessary to verify the claimed corrosion resistance of the particular coating(s).
Salt spray testing is an accelerated corrosion test that produces a corrosive attack on the coated samples in order to predict its suitability for use as a protective finish over the expected lifetime of the product.
The specifications of the test chamber construction, the testing procedure and its parameters are all standardised under national and international standards.
Salt Spray Testing Standards
We test to the following standards:
- ASTM B-117 ASTM B117 – Standard Practice for Operating Salt Spray (Fog) Apparatus
- EN ISO 9227 – Corrosion Tests in Artificial Atmospheres – Salt Spray Tests
- EN ISO 7253 – Paints & Varnishes – Determination of Resistance to Neutral Salt Spray (fog)
- EN 60512-11-6 – Connectors for Electronic Equipment – Tests and Measurements
- EN ISO 4541 – Metallic and other Non-Organic Coatings – Corrodkote (CORR) test
- DIN 50 021 – Copper Chloride Acetic Acid Salt Spray Test (CASS)
- ISO 3769 – Corrosion Testing of Metallic Coatings – Acetic Acid Salt Spray Test (AASS)
- FORD FLTM BI 103-01 – Salt Spray Resistance Test for Painted Panels & Parts (Ford)
- GM4298P – Salt Spray / Mist Testing (General Motors)
The Different Types Of Salt Spray Testing
There is a wide range of salt spray test options, depending upon the base material, coating, and most importantly the standard you are testing to.
The most common is Neutral Salt Spray (NSS) – the baseline of salt spray testing – followed by Acetic Acid Accelerated Salt Spray (AASS), and Copper Acetic Acid Accelerated Salt Spray (CASS).
Neutral Salt Spray (NSS) Testing
- Used for Standards: ASTM B117 & BS EN ISO 9227
- Neutral 5% sodium chloride solution – with a pH value of 6.5-7.2
- Applied to metals and their alloys, metal coatings (anodes and cathodes), conversion coatings, anodic oxidation coatings, and organic coatings on metal materials
- Results are represented generally as testing hours without the appearance of corrosion (e.g. 720 h in NSS according to ISO 9227).
Acetic Acid Accelerated Salt Spray (AASS)
- Used for Standards: ASTM G-85
- Acidified 5% sodium chloride solution with the addition of glacial acetic acid in the pH range of 3.1 to 3.3
- For testing decorative coatings of copper + nickel + chromium, or nickel + chromium; also used for testing anodic coatings on aluminium.
Copper Acetic Acid Accelerated Salt Spray (CASS)
- Used for Standards: ASTM B 368
- Acidified 5% sodium chloride solution with the addition of glacial acetic acid and copper chloride in the pH range of 3.1 to 3.3
- For testing decorative coatings of copper + nickel + chromium, or nickel + chromium; also used for testing anodic coatings on aluminium.
Filiform Corrosion Testing
- Used for standards: ASTM D 2803
- Filiform corrosion occurs on metallic surfaces that are coated with a thin organic film, typically 0.05 to 0.1 mm (2 to 4 mils) thick, when exposed to a warm, humid atmospheric air. Filiform corrosion always starts at coating defects such as scratches and weak points such as cut edges and holes
- For testing decorative coatings of copper + nickel + chromium, or nickel + chromium; also used for testing anodic coatings on aluminium.
Samples That Can Be Evaluated
Substrates and coatings suitable for testing include:
- Painted substrates (powder coated / wet paint systems)
- Pre-treated substrates under a powder coating / paint system (tested for longevity)
- Complex high-build paint systems (for superior corrosion resistance)
- Zinc and zinc-alloy plating (see also electroplating). See ISO 4042 for guidance
- Electroplated chromium, nickel, copper, tin
- Coatings not applied electrolytically, such as zinc flake coatings according to ISO 10683
- Organic coatings.
And those not usually suitable:
Hot-dip galvanized surfaces are not generally tested in a salt spray test (see ISO 1461 or ISO 10684). Hot-dip galvanizing produces zinc carbonates when exposed to a natural environment, thus protecting the coating metal and reducing the corrosion rate.
However, painted surfaces with an underlying hot-dip galvanized coating can be tested according to this method. See ISO 12944-6.
The zinc carbonates are not produced when a hot-dip galvanized specimen is exposed to a salt spray fog, therefore this testing method does not give an accurate measurement of corrosion protection. ISO 9223 gives the guidelines for proper measurement of corrosion resistance for hot-dip galvanized specimens.